Written by: Chad Jenkins, PHD, PAS
KEY TAKEAWAYS IN THIS ISSUE OF TECHNICAL TOPICS:
- Timing of corn silage harvest should be determined by both whole-plant moisture and milkline
- Target chop length should be determined and monitored throughout harvest
- Kernel processing is critical and has significant economic impact
- Rate of fresh silage delivery may be used to determine tractor weight needed for packing
- For silage inoculant to be effective, proper handling and application rate are crucial

‘Where did the summer go?’ seems to be a phrase often uttered at this time of year. Consequently, for those of us in the animal feeding business, the phrase also signals the rapid approach of harvest time. While many of us may already have hundreds of thousands of tons of corn silage harvested under our belts (or more accurately, tarp ‘n’ tire), it’s always advisable to review the fundamentals and latest research before the first chopper rolls. Proper silage processing and storage ultimately maximizes the amount of milk that it will support for the year to come!
CONTROL POINT 1: TIMING
Timing of corn silage harvest is a critical balance between maximizing yield and ensuring adequate moisture for effective fermentation, fiber, and starch digestibility. In a recent round-table discussion with the Midwest contingent of Standard Dairy Consultants, it was noted that the corn kernel seems to have matured faster than the rest of the plant in recent crop years, resulting in reduced starch digestibility, despite being taken at recommended moisture levels. While the staple rule-of-thumb has been to harvest at 65% whole-plant moisture (35% DM), it is also advisable to account for the progression of the “milkline”. The milkline forms between the darker starch (hard endosperm) at the top of the kernel and the lighter “dough” (liquid endosperm) at the bottom of the kernel. At about one-half milkline, starch content and digestibility are optimized. One-half milkline may not always equilibrate with whole-plant moisture, which emphasizes why this tried-and-true benchmark should not be overlooked.
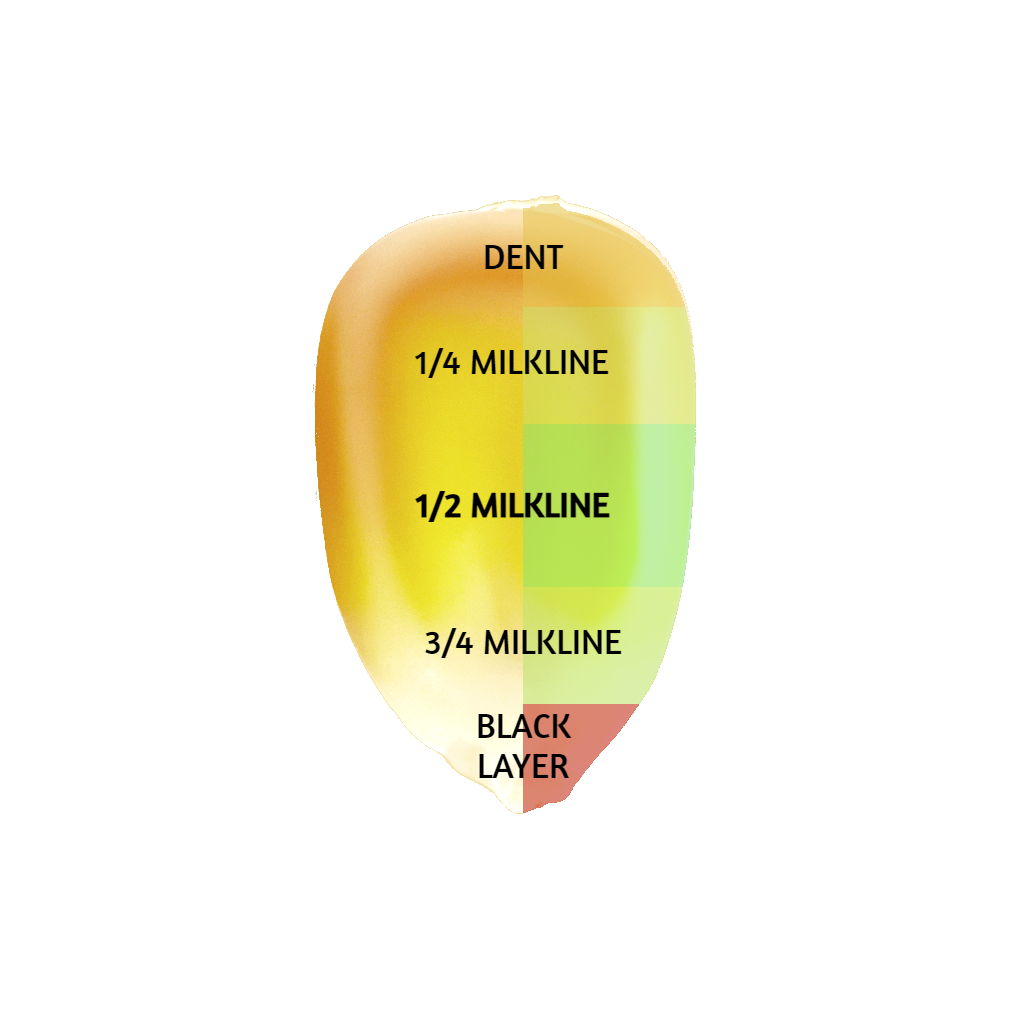
Conversely, while milkline may be in the ideal location, whole-plant moisture should not be neglected due to the potential for excess leachate which leads to nutrient loss. If the kernel has reached one-half milkline, the moisture content needs to fall below at least 70% before silage harvest should begin.
CONTROL POINT 2: CHOP LENGTH
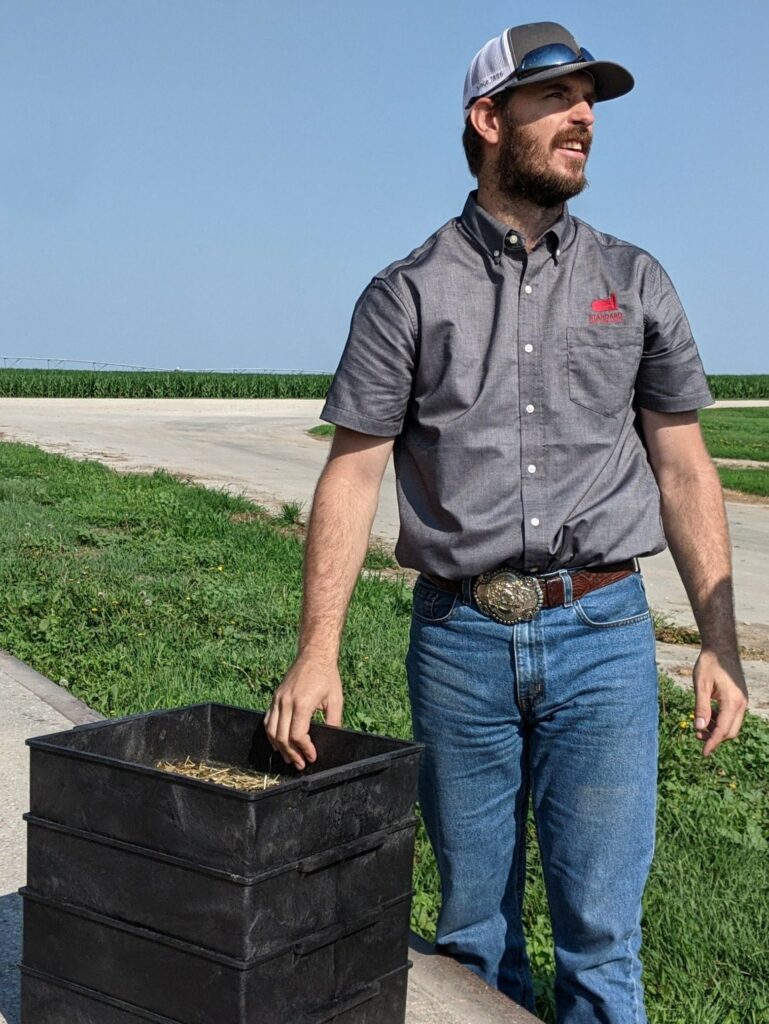
The second control point to be monitored is particle length of the plant as it is chopped. Extensive research by the Miner Institute has revealed that particle length strongly correlates to eating time, which in turn relates to cows’ time budget; too much time spent eating takes away from other activities such as resting and ruminating, while too little time is linked to increased passage rate and reduced digestion (Grant, 2023). In general, the chopper should be set to 5/8” to 7/8” theoretical length of chop (TLC) for adequate particle length. A great way to monitor that TLC is within an acceptable range is to measure particle size distribution with a Penn State Particle Separator (“shaker box”). Loads being dumped at the dairy should be periodically checked, with an ideal particle distribution of approximately:

Special emphasis should be given to the 19 mm screen and pan. Excessive particles on the 19 mm screen can result in increased sortability and eating time. Additionally, a buildup of fine material in the pan equates to a reduction in physically effective fiber. If it is found that loads are consistently falling outside of these ranges, especially with the top screen exceeding 18% or pan exceeding 10%, an adjustment should be made to the TLC with the chopper. It is also important to consider the ideal distribution of particle sizes depending on the makeup of other ingredients in the ration – for example, in years where hay is sparse and corn silage will comprise a larger proportion of the ration, more length will be desirable to provide additional effective fiber.
In the sometimes-unavoidable situation where corn silage must be taken drier (<60% moisture) and relatedly, more mature than desired, the TLC should be reduced to 3/8” to 1/2”. A more mature corn plant will accumulate undigestible fiber (uNDF240) that contributes to lower dry matter intakes and milk yield, especially with increased particle length. Reducing the particle length of higher uNDF240 silage will help bolster dry matter intake. Additionally, if the chopper is not equipped with a kernel processor, shorter TLC (3/8” – 1/2”) should be considered so that the kernels have an increased chance of being broken by the rollers.
CONTROL POINT 3: KERNEL PROCESSING
One of the most critical factors to maximize the amount of milk your corn silage will support is kernel processing. When the kernel is pulverized, bacteria responsible for the ensiling process have increased access to the protein (referred to as “zein” or “prolamine”) that surround the starch granules within the kernel – this allows for more breakdown of this protein via fermentation, eventually increasing the accessibility in the rumen for digestion.
To highlight the importance of kernel processing from a financial perspective, consider the potential impact on fecal starch (% of starch in manure). Let’s assume that a 1,000 cow dairy is able to reduce fecal starch from 5% to 3% by improving kernel processing. When feeding 55 DM lbs of a diet that is 25% in starch, 5% fecal starch equates to 1.36 lb of corn per day in the manure vs. 0.81 lb with 3% fecal starch — the difference is the equivalent of $17,500 per year of corn in the manure with $5.00 corn! In addition, every 1% increase in fecal starch above 3% represents about 0.7 lb of milk loss. In this scenario, that would be about 500,000 lb of milk in a year worth $75,000 ($15.00 milk)!
A simple way to monitor kernel processing during harvest is with the cup method. First, treat yourself to a 32 oz Diet Coke (and save the cup)! Second, while silage loads are being dumped, take a representative sample, filling the cup. The material may then be spread on a table or, to make things easier, sifted by shaking with the Penn State Box. Third, separate the corn kernels – the rule of thumb is that no more than two, 1/2 sized kernels should be found in 32 oz of fresh sample. If more than two are found, let the financial scenario above encourage you to have a discussion with the chopper.
CONTROL POINT 4: PACKING AND COVERING
Packing and covering are necessary for the elimination of oxygen, which supports proper fermentation. The two key factors for achieving the densest pack possible are layer thickness and weight. As each load of fresh silage is brought in, no more than a 6” layer should be added to the pile. Weight needed to compress these layers may be determined by the tons of silage chopped per hour; in general, about 800 lbs for each ton is required. For example, imagine we counted ten truckloads of fresh silage in one hour, each weighing fifteen tons (10 loads × 15 tons = 150 tons/hour). Therefore, 150 tons/hour × 800 lbs ÷ 2000 = 60 tons of total tractor weight on the pile. On drive-over piles, remember that the effectiveness of packing is reduced on steep slopes. For this reason (as well as tractor safety), side slopes of greater than 3:1 (3 ft horizontal per 1 foot vertical) should be avoided.
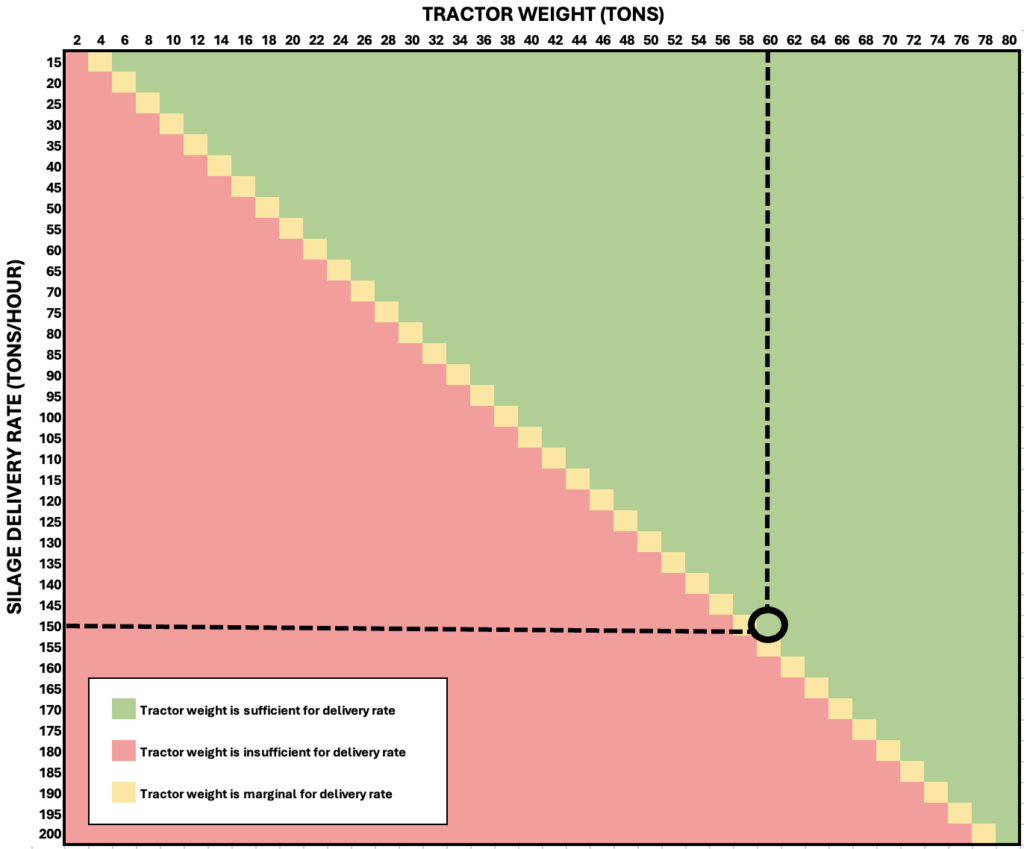
Finally, high-quality plastic silage tarp of 6 to 8 mil should be used to cover the pile. In addition, an oxygen barrier film may be used as an additional layer (under the tarp) to prevent spoilage in the top few feet of the pile where silage is not as dense. Before chopping begins, lining the sides of concrete bunker walls with plastic tarp is advisable so that any future rainwater may run down the sidewalls and drain. Tires or sandbags should be used to thoroughly cover the tarp, holding it in place and preventing additional oxygen from entering.
BONUS CONTROL POINT: SILAGE INOCULANT
Research has demonstrated that using silage inoculant prevents dry matter losses by increasing the rate at which pH is reduced in the fermentation process and by slowing spoilage at feedout. If you have decided to apply a forage inoculant during harvest, below are a few tips and tricks to ensure proper application and return on your investment.
Because inoculants contain living organisms, they must be stored in cool temperatures prior to use (fridge or freezer). Those that have been stored in the freezer should be thawed at room temperature or in cold water. When mixing before use, cold water should be used because hot water can kill the bacteria. Consider using an insulated inoculant applicator tank that is mounted away from the engine and exhaust of the chopper so that it stays cool. Mixed product should be used within 48 hours (if kept cool).
Application rate should be checked and re-checked – the typical application rate for homolactic bacteria is 100,000 colony forming units (cfu) per gram of fresh forage, and inoculant suppliers often advertise the number of treated tons per package. Based on the rate of silage harvest, one can work backward to determine if inoculant is being applied as expected. Continuing with the previous example, imagine we counted ten truckloads of fresh silage in one hour, weighing about fifteen tons each. This equates to about 2.5 tons/minute of silage chopped (10 loads × 15 tons ÷ 60 minutes). Therefore, if we are using an inoculant canister that is advertised to treat 500 tons, the chopper should go through a canister’s worth of inoculant in 3 hours and 20 minutes of chopping (500 tons ÷ 2.5 tons/minute = 200 minutes ÷ 60 = 3.3 hours). If it is found that inoculant is not being used at the rate expected, check to make sure that spray nozzles are not plugged and that the applicator pump is set as expected.
In summary, corn silage harvest is an exciting time of year and many of the decisions we make now will have a significant impact on the productivity of the dairy for the year to come. So, remember the fundamentals, be safe, and chop away!